01.07.15
Are we looking at a new age of elegant, visually appealing rail buildings and trackside structures?
Source: RTM Jun/Jul 15
The new roof structure at Manchester Victoria station is a fantastic example of what is possible with modern steel manufacturing techniques; it joins the western concourse at King’s Cross as a notable visual design using structural steel and daylight to introduce modern organic lines into a rail structure for dramatic effect. Matthew Pritchard of specialist steel bending company Barnshaws, which manufactured the beams for Manchester Victoria, says we can expect this to influence more rail structures in the future.
It’s strange that steel bending, combined with some inspirational design, means future rail station designs and refurbishments can be beautiful again. It seems we can look forward to more railway architecture with some style and bravura, thanks to the type of steel bending that is now commercially viable.
Greg North, commercial director for Barnshaws, said: “There are good structural reasons for including elegant compound curves and shaped steel roof supports, but the cost has previously been judged prohibitive and during the 1970s and 80s the vogue was for steel and concrete boxes. Barnshaws use a variety of extremely efficient and accurate methods of bending, forming and shaping steel tubes, box sections, beams and plates so designers can now express themselves without breaking the construction budget. In addition to other structural buildings, we are also producing small shelters and electrification gantries that are lighter, stronger and more aesthetically pleasing.”
Manchester Victoria, as an example, includes a state-of-the-art roof constructed around 15 curved steel ribs. The task of producing the curved structure for the new £16m roof was partly carried out at the nearby Barnshaws production facilities. The intention is to provide a modern and bright feeling to the new concourse, which has been designed to be sympathetic with the original Grade II listed building and also to provide sufficient capacity for future expansion.
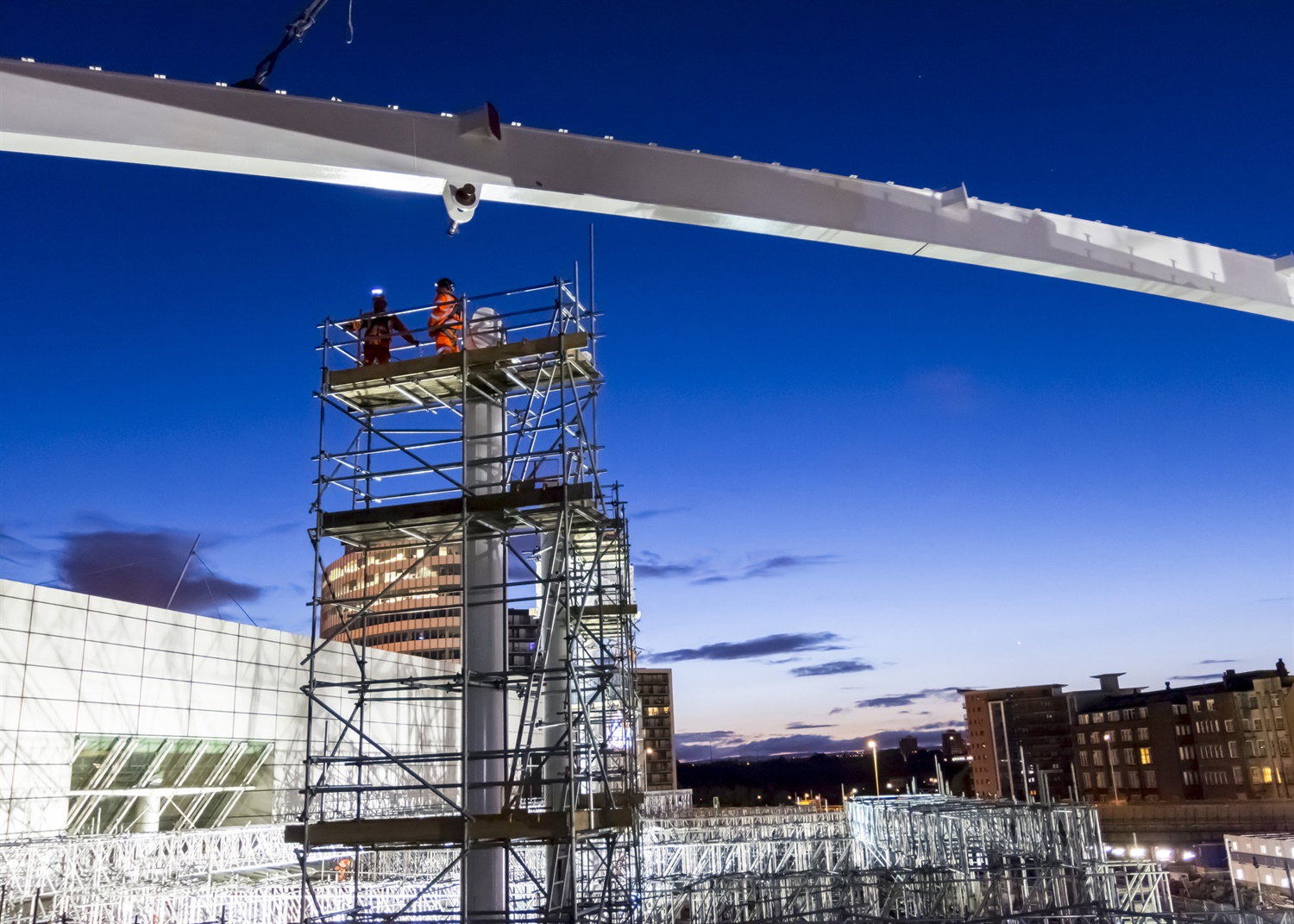
For the main contractor, precision and timing were key to overall success, as the design of the new roof was always going to pose some tough challenges for the fabricators, Severfield (UK). Each rib has a unique design, not only in length but also in width, depth and curvature, so the actual manufacturing required a high level of precision. In addition, the ribs had to be made in sections up to 20 meters in length and then transported to the site before final assembly and installation (the full story is in the Aug/Sept 2014 edition of RTM).
Engineers from the two companies worked together to develop the design so it could be installed in the most efficient manner. This ended up requiring two of the largest cranes in the country and some millimetre-perfect construction as well as precise timing.
North added: “We have worked with Severfields on a large number of projects and we understand each other’s capabilities and strengths. For one particular part of the project, we were able to provide 350mm square hollow section (SHS) steel that was curved to a 7,000mm radius at certain points with no distortion to the section, thanks to our specialised methods of bending.”
In fact, all of the SHS steel required three or four different radii within each length, but this is all within the capability of Barnshaws and the engineering team, who were able to deliver these components on time. The second part of the project required steel plate measuring up to 550mm wide by 50mm thick to be curved to various radii to make the larger sections of each rib.
Each plate section was curved to a specific set of dimensions to allow it to be assembled into a curved box-section by Severfield. These were then transported to the station site, where they were welded together to create the complete rib, which was then carefully positioned and installed. Each of these unique ribs required considerable precision and tight tolerances to ensure the installation process went smoothly.
Most of the curved beams were installed using the UK’s largest telescopic crane, a 1,200-tonne behemoth, while rib 9 (the largest, at 96m long and nearly 86 tonnes), was installed using a 750-tonne crawler crane, which is one of Europe’s largest of its type.
This in itself created complications due to the live tracks that run beneath the new roof structure and the whole installation process required close cooperation with Network Rail. In this way, the short periods during which the tracks could be made safe were utilised as efficiently as possible, ensuring the roof structure was installed on schedule.
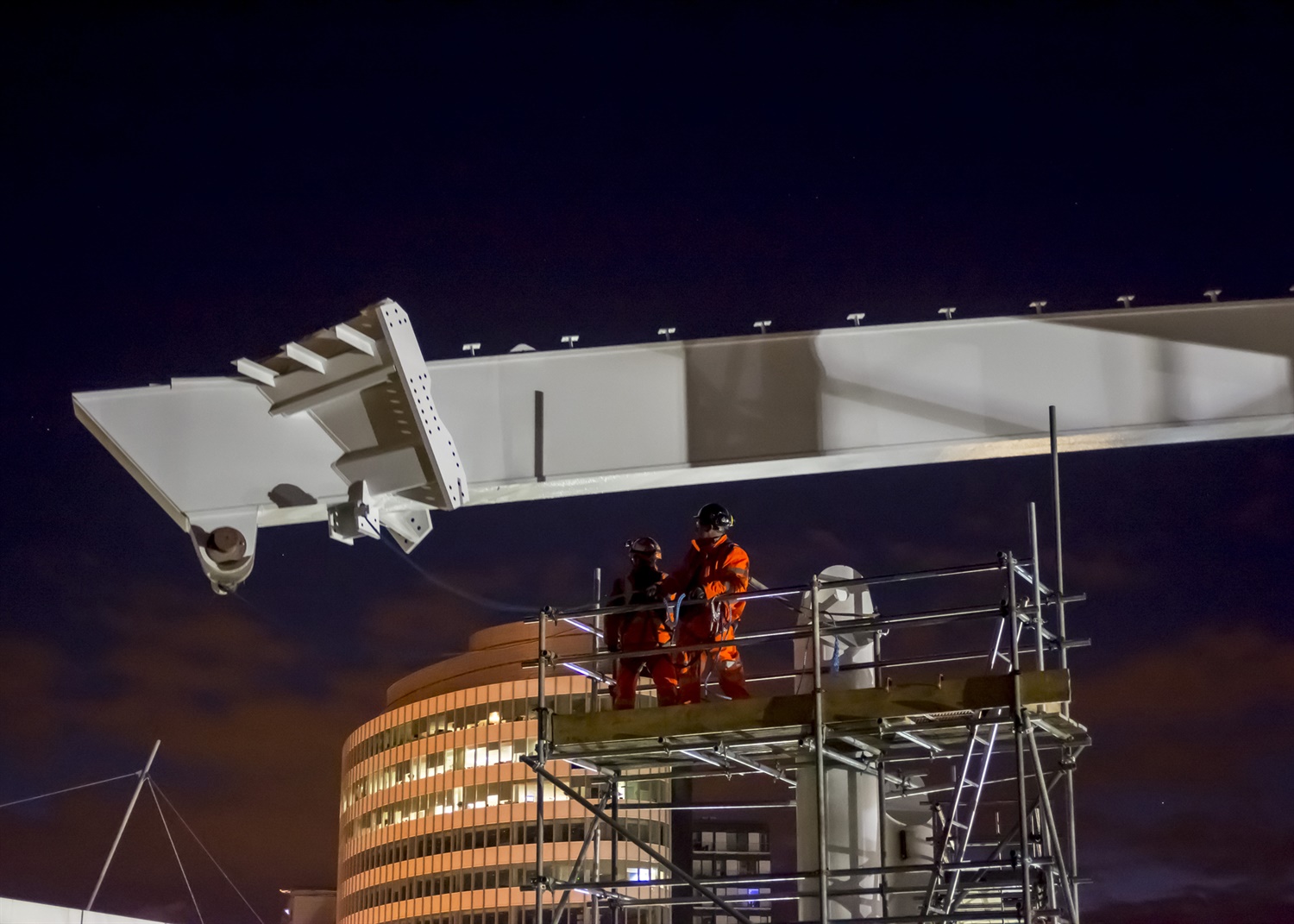
With the main ribs installed, the smaller subsections could be fitted to support almost 400 ETFE (ethylene tetraflouroethylene) panels, similar to those used in the Eden Project and Manchester Piccadilly station. As with the steel sections, each polymer roof panel has a unique shape and relies on the precision of the steelwork to ensure a perfect fit.
North concluded: “The design of this project has posed some challenges to all of those involved in making it a reality, but together we have succeeded in delivering a fantastic structure that will greet everyone visiting Manchester Victoria. The drive to create more beautiful railway structures and buildings definitely has momentum now, as we are also supplying anchor booms to support the overhead cables for the electrification of the Great Western Railway from London to Cardiff. Not only are these stronger than box section alternatives of comparable weight, but they are faster to erect and, to my eye, look far nicer. ”