21.09.17
Ballast or slab?
Source: RTM Aug/Sep 17
As HS2 moves forward, William Powrie, professor of geotechnical engineering and dean of the Faculty of Engineering and the Environment at the University of Southampton, considers the arguments for and against using ballasted or slab track in high-speed rail.
In traditional railway track, the rails are supported and held apart by sleepers or ties, which rest on and are embedded in a coarse granular aggregate known as ballast. Over the decades, materials and components have changed (e.g. the iron or steel used for the rails; the fastenings; the rail profile from bullhead to flat-bottomed; timber sleepers to reinforced concrete; and railpads have been introduced), but the underlying principles of the system have remained the same.
The role of the ballast is to provide a stable support for the track. The depth of ballast is specified so as to reduce the stresses transmitted to the subgrade (the underlying soil) to acceptable levels – low enough not only to prevent failure, but also to keep the rate of accumulation of permanent settlement over millions of loading cycles low enough to be dealt with by periodic maintenance. Differential settlement, which results from unpredictable local variations in dynamic train loading or track support conditions, is usually the main concern. The ballast must also be able to resist train loading, both longitudinal (e.g. on acceleration and braking) and lateral (e.g. curving), as well as temperature-induced rail buckling.
Ballast is attractive because it is relatively inexpensive and enables the track to be adjusted – either back to its initial position, or to a new layout. This attraction is also its weakness; because the track is not rigidly held in position, it gradually loses its line and level and needs periodic maintenance to restore the design geometry. Predicting the rate at which the geometry of ballasted track deteriorates theoretically is not possible: the various formulae are all empirical and apply only in the conditions for which they were developed. However, it is generally accepted that train speed, axle load, cumulative load and subgrade support conditions all play a role.
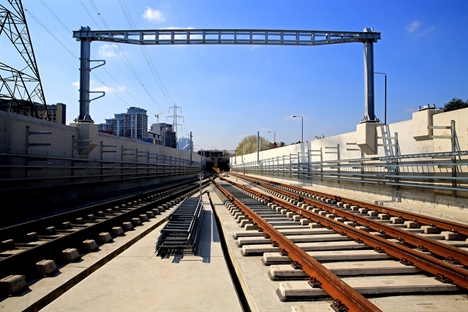
© Crossrail
Growing popularity of slab track
As train speeds, axle loads and traffic intensity increase, there comes a point at which the maintenance requirement for ballasted track is excessive and a more robust solution becomes financially viable. The approach adopted is usually to mount the rails on a continuous or near-continuous reinforced concrete slab, known generally as slab track. Slab track has been used increasingly in recent decades on high-speed railways around the world. Where ground conditions are poor, the slab track may be supported on piled foundations, forming what is essentially an in-ground viaduct. For example, HS1 crosses Rainham Marshes on a 7km-long piled raft. Elsewhere in the UK, slab track has been used mainly in tunnels, where limited clearances mean that the design geometry must be maintained within tight tolerances.
Ballasted track has a lower capital cost but may have a higher maintenance cost than slab track. Therefore, an analysis of whole-life costs will give a ‘crossover point’ (either in time or cumulative load), after which the total cost of a slab track system (adjusted to net present values using an appropriate discount rate) will be less than that of ballasted track. In principle, such an analysis could be used to inform a decision about whether to install slab or ballasted track in any particular set of circumstances. Work for the DfT suggests a crossover point of more than 90 years for four out of five slab track systems considered, assuming ‘typical’ subsoil conditions and 20 equivalent million gross tonnes per annum (EMGTpA) of traffic loading (similar to the West Coast Main Line (WCML): projected traffic on HS2 is much greater, at 62 EMGTpA).
However, the result of such an analysis is only as good as the assumptions made concerning usage and financing costs, and – critically – deterioration and maintenance rates. Data from the WCML north of Carlisle suggest that ballast maintenance may be needed more frequently on a clay subsoil than on sand. As the methods used to assess track geometry deterioration rates are experience-based, the margin of error is huge. In a phrase generally attributed to Nils Böhr or Yogi Berra, “prediction is very difficult, especially about the future”.
A further problem with ballasted track at high train speeds is that ballast grains can become airborne as a result of a combination of air turbulence and groundborne vibration (a phenomenon known as ballast pickup or ballast flight), although this can probably be prevented by good ballast specification/management and aerodynamic design of the train underbody.
And then there is the issue of noise. It is generally held that slab track may be 3-4dB noisier than ballasted track, but again the scope for variation is huge. Ballasted track varies considerably, with rail pad stiffness being a key parameter. The low fastener stiffness on slab track is the main reason for its higher noise levels, with absorption of sound by the ballast accounting for only about 1dB. Treatments for noise from slab track include absorptive panels and rail dampers.
In planning a new railway, the main factors to be considered when deciding on the track form include:
- Train speed and intensity of loading, as already discussed
- The strength and stiffness of the subsoil (softer soils might require a stiffer track form to guard against resonance or ‘critical velocity’ effects)
- The performance of unpiled slab track on the highly plastic clay subsoils found across much of the southern UK. These soils shrink and swell significantly when their water content changes. The Chinese high-speed line from Dalian to Harbin had to be rebuilt on viaducts over 20% of its length when the original slab track design was unable to cope with frost-induced heave (swelling) of the subsoil (resulting in a total of 70% on viaduct)
- Whether the performance of ballasted track could be simply and cost-effectively improved, for example by an asphalt under-ballast layer. Measures such as under-sleeper pads, changing the ballast grading, reducing the ballast shoulder slope, confining the ballast or adding random fibre reinforcements could extend the time between maintenance interventions for ballasted track by a factor of three or more
- The likelihood of a change in track layout being required part-way through the design life of a slab track installation (for example, the slab track in Southampton Tunnel originally laid in the 1970s was replaced in 2010 to enhance the loading gauge)
- If a route has a large number of tunnels and viaducts, it might well make sense to build it all on slab track to avoid high-maintenance transition zones between different track forms
- Whether the projected intensity of use will allow the downtime needed for maintenance of a ballasted track
- Affordability at the time of purchase, which may well be the ultimate decider.
Top Image: © Geoff Watson
For more information
W: www.southampton.ac.uk