16.12.15
Could confidential reporting have prevented the Deepwater Horizon tragedy?
Source: RTM Dec/Jan 16
Chris Langer, scheme intelligence manager at CIRAS, the confidential incident reporting and analysis system for the rail industry, thinks the oil and gas industry could learn something from the rail industry’s adoption of confidential reporting after Ladbroke Grove.
Eleven lives lost. Five millions barrels of oil spilled into the sea. Approximately $27bn spent so far by BP in fines, economic claims, disaster response efforts, and clean-up and restoration programmes. And no independent, confidential reporting system for staff to use in the oil and gas industry.
This last fact is by no means irrelevant, or inconsequential. Could confidential reporting have actually helped avert the disaster?
A parallel can be drawn here with the rail industry. After 31 lives were lost in a train accident at Ladbroke Grove in 1999, the rail industry began to fully embrace the notion that confidential reporting for safety could help drive an improvement in safety culture at a national level.
Tarnished reputation
It’s been five years since the explosion at the Macondo oil rig and the subsequent environmental catastrophe in the Gulf of Mexico. But residents and activists in the area surrounding the Gulf of Mexico are still finding oil on beaches, land and in the water. There has been a suggestion from the National Wildlife Federation that up to 20 species are still affected. Last year, dolphins along Louisiana’s coastline were found dead at four times the normal rate. Some fishermen are also finding their nets are coming back empty – though this may be hard to link directly with the spill, and BP disputes the evidence, it is a reminder of the potential loss to economic livelihoods.
BP is insisting things are ‘getting better’ despite a high degree of public scepticism, and the scientific evidence refuting this view. One thing is certain: BP’s costs associated with the disaster are steadily increasing, even now, and it is clear massive reputational damage has been inflicted. No amount of carefully crafted corporate PR spin from BP can reverse the negative trajectory of events. For the time being at least, it doesn’t look as though public opinion can be shifted that much either. The recovery from a tarnished reputation is, at best, a long and painful process. BP has said its US subsidiary may even go bankrupt if it cannot afford the fines, which continue to rise.
It may well be perceived as preaching from the side lines, but I am persuaded that confidential reporting could have been critical in preventing both loss of life and environmental catastrophe in the Gulf of Mexico, as well as leaving BP’s reputation intact. Of course, we can’t know for sure. We can’t travel back in time and run an experiment under different conditions. There’s no way of knowing if the critical information needed to prevent disaster would have surfaced if the oil and gas industry had subscribed to confidential reporting. There are, however, reasonable grounds for thinking it could have made all the difference.
The troubling symptoms of a disaster-in-the-making may well have been picked up far earlier through the mechanism of confidential reporting. The rail industry isn’t perfect by any means, but it does provide a safety net for operators by allowing hidden safety information to surface.
President Barack Obama created the National Commission in 2010 shortly after the disaster for the purpose of independently and impartially investigating the causes of the oil spill in the Gulf of Mexico. One of the conclusions in the final report was: “There are recurring themes of missed warning signals, failure to share information, and general lack of appreciation for the risks involved.”
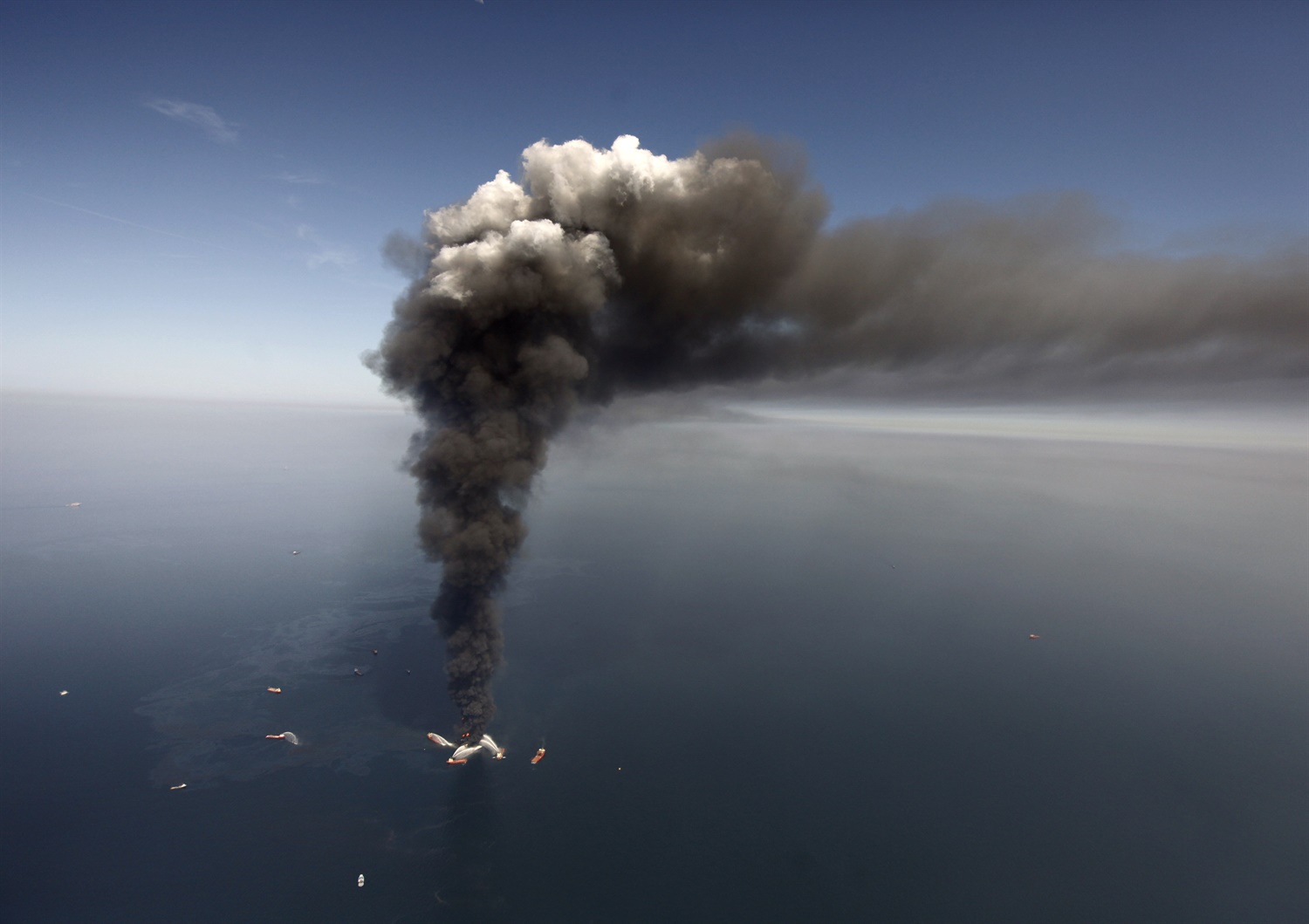
‘Risk factors, oversights, and outright mistakes’
Persevering with the report is a rewarding exercise. The more you read, the more you realise that all the knowledge needed to prevent the catastrophe was close at hand, just not communicated, or acted upon effectively enough. The National Commission pulls no punches when they say in the report: “The well blew out because a number of separate risk factors, oversights, and outright mistakes combined to overwhelm the safeguards meant to prevent just such an event from happening. But most of the mistakes and oversights at Macondo can be traced back to a single overarching failure – a failure of management.”
In other words, there was a clear failure to instil good safety culture, and key safety defences had been steadily eroded over time, making such a disaster more or less inevitable. Unchecked failings may well have made the disaster inevitable, but this shouldn’t be equated with it being unpreventable.
So how were these safety defences so effectively overwhelmed? How did the crew on the oil rig come to describe it as ‘the well from hell’, while BP’s vice-president of drilling operations said it was “…the best performing rig that we had in our fleet and in the Gulf of Mexico”?
Divisions in thinking between frontline staff and management
You would be forgiven for thinking they were talking about different oil rigs altogether. The oil rig crew and senior management were not only talking a different language, they were inhabiting different safety worlds. This phenomenon is by no means peculiar to the world of oil and gas – the same divisions in thinking between frontline staff and management exist in other industries too. It would be puerile to think the rail industry were in any way immune.
What we know from the National Commission’s report is that key safety systems were intentionally switched off. For starters, the physical alarm system on the rig was disabled a year before the disaster. A crucial safety device to shut down the drill shack if dangerous gas levels were detected was also disabled, or ‘bypassed’. This last fact hadn’t gone unnoticed – indeed, the chief technician had previously protested to his supervisor. The response he received was truly astonishing, indicating a much wider malaise: “Damn thing been in bypass for five years. Matter of fact, the entire fleet runs them in bypass”.
In other words, the practice of bypassing a critical safety system was set up to be the default in many other locations too.
But the catalogue of management failings doesn’t end there. There was no procedure for running, or interpreting, what in the oil and gas business is called the ‘negative pressure test’ to show the well was safely sealed with cement. So the crew weren’t able to decipher critical data that would have alerted them to the danger signs. To make matters worse, there was no procedure for calling back to shore for a second opinion about confusing data. Finally, there was no formal training for the rig crew, especially in response to emergency situations.
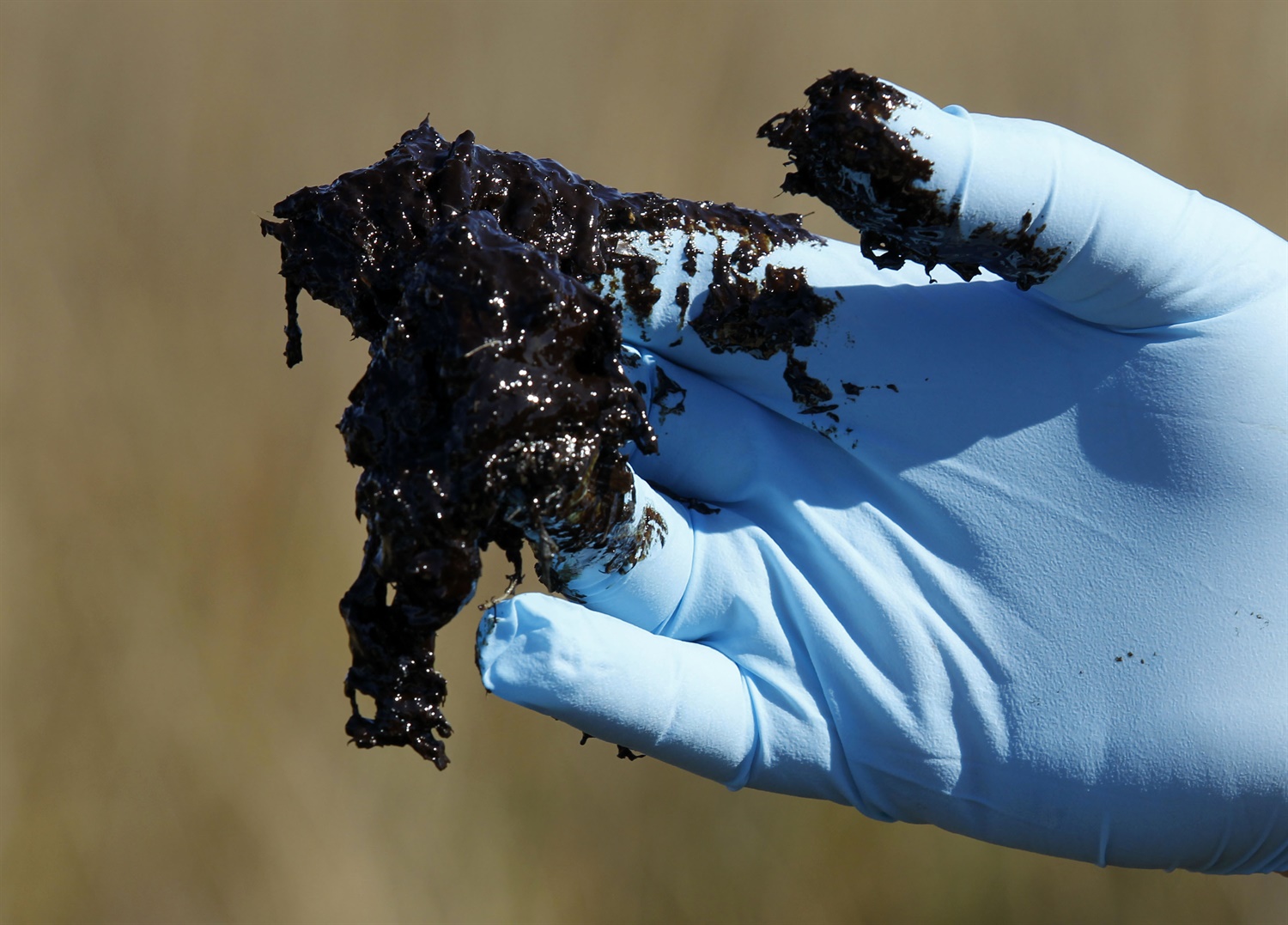
Failing to learn from a near-miss
To my mind though, by far the biggest failing was the failure to learn from a near-miss incident in the North Sea just four months earlier. Learning from this incident (at a rig also run by BP’s contractor Transocean) had the clear potential to prevent the loss of 11 lives and the environmental disaster in the Gulf of Mexico. The basic facts of the two incidents were essentially the same, but the North Sea near-miss didn’t reach the level of catastrophic blowout.
Tragically, the lessons from the North Sea incident weren’t communicated to the crew at Deepwater Horizon. The critical learning remained frustratingly ‘locked away’ in the system. Had this learning reached the right personnel in time, it may have prevented the disaster. An ‘operations advisory’ with the critical information was sent to some of the fleet in the North Sea, and a PowerPoint presentation was created for the purposes of learning from the incident. Neither made it to the Deepwater Horizon crew. In the digital age, when all this information could have travelled thousands of miles at the touch of the ‘send’ button, this is especially difficult to accept.
Learning about safety culture from the rail industry
Creating the right environment for reporting safety issues is absolutely essential. The Deepwater Horizon rig crew were aware of unsafe practices, but afraid to report internally, despite referring to their workplace as ‘the well from hell’. When they did voice concerns, it was met with a complacent response, fuelling an apathy towards safety culture.
Fully sharing critical near-miss incident information with everyone who needs to know is also fundamental to ensuring safe operations. The Deepwater Horizon crew clearly needed to know about the North Sea incident in similar circumstances, and to learn from the mistakes there.
Confidential reporting acts as an additional line of defence where internal reporting systems fail to fully meet these two objectives. Where trust is in short supply, for whatever reason, confidential reporting can help facilitate the resolution of long-standing safety issues. Sharing the lessons learned from wider industry is critical for ensuring a more proactive safely culture prevails. Like the rail industry, the oil and gas industry could whole heartedly embrace confidential reporting to make a step change in safety culture.
About CIRAS
CIRAS is a confidential incident reporting and analysis system, which has been operating since 1996.
It offers a corporate safety net that ensures safety, health or other concerns are captured where they otherwise might be lost, or remain unaddressed. With CIRAS’ help, these concerns are investigated to a satisfactory conclusion.
CIRAS offers an alternative, truly independent, confidential reporting line to a range of transport modes and infrastructure organisations. Staff can call knowing their identity will never be shared. The aim is to exploit the opportunity to learn from every report received. Through an engagement programme, newsletters and website, the lessons learned and the actions taken are shared.
Tell us what you think – have your say below or email [email protected]