01.05.15
‘They don’t make trains like this anymore’
Source: RTM Apr/May 15
RTM’s Sam McCaffrey visited the Vivarail depot at Long Marston to see the prototype D-Train in the middle of the conversion process.
“There is nothing quite as exciting as this in the industry at the minute.”
Those are the words of Steve Rowell, general manager of Vivarail, who is overseeing the conversion of the old London Underground D78 electric stock into the new D-Train DEMU.
Rowell has a lengthy rail industry background, with 21 years at Tyne & Wear Metro culminating in three years as engineering director before heading off to gain some heavy rail experience at East Coast as the head of quality and compliance for engineering.
While at Metro he was involved in the three-quarter life refurbishment of the fleet, which caught the eye of Adrian Shooter, who recruited him into his current role.
“This Vivarail concept is one of those ideas that you look at and it’s a once-in-a-lifetime opportunity,” he said. “Everyone who I’ve interviewed, everybody who has come on board, have all opted to do so on the basis that there is nothing quite as exciting as this in the industry at the minute. We can all go work for other TOCs or other ROSCOs or rolling stock manufacturers, but to be doing something like this at this point in time…it’s different.”
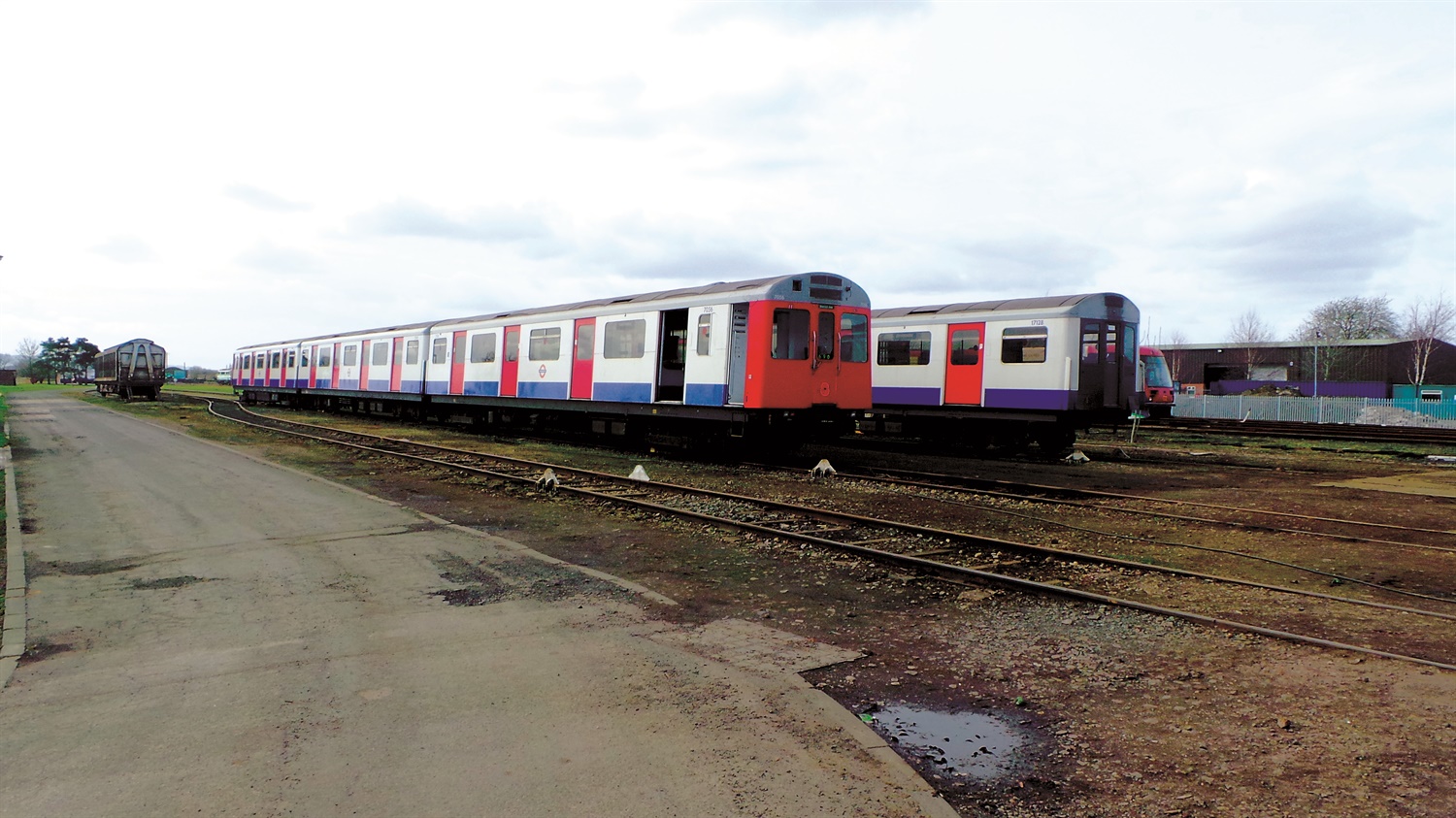
Prototype
What’s so different about it? To explain, Rowell walked me through the Vivarail facility at Long Marston, showing off the prototype in the midst of the conversion process.
When I arrived at the end of March, the team had just finished stripping the interiors and everything off the underside of the carriages, including the bogies, leaving a hollow aluminium shell in London Underground colours.
From the prototype, one set of bogies has been delivered to Strukton Rail in the Netherlands (who are supplying the traction control system) and another to Revolve Engineering in Essex (who are supplying the diesel engines) for the next stage of systems integration.
Rowell said Strukton has also received two separate traction motors so it can make sure they can be “as much finessed as possible”. This will also help when the time comes for track testing, as any tweaks can be trialled in the Netherlands before applying them to the prototype.
Strukton Rail’s traction systems are based on Insulated Gate Bi-polar Transistor (IGBT) technology, designed for smooth acceleration and energy efficiency. D-Trains will be equipped with an IGBT DC chopper to provide the required motor current, and the traction control electronics and battery charger will be integrated in one box.
At Revolve Engineering, the power raft frame has completed its tolerance testing and welding, and is currently being galvanised. As part of the low maintenance strategy espoused by Vivarail at every juncture, the individual units can be replaced in only 10 minutes in ‘mini-depots’ at local junctions or termini. Rowell estimates that a full engine change will be needed every 150,000 to 200,000 miles.
Rowell said: “It’s all stop-start technology too; when the engine is not needed, it will shut down. We’ll typically always have one engine going, in most instances, for battery recharging – but fundamentally when they’re not needed, then gensets will shut themselves down, and then restart automatically.”
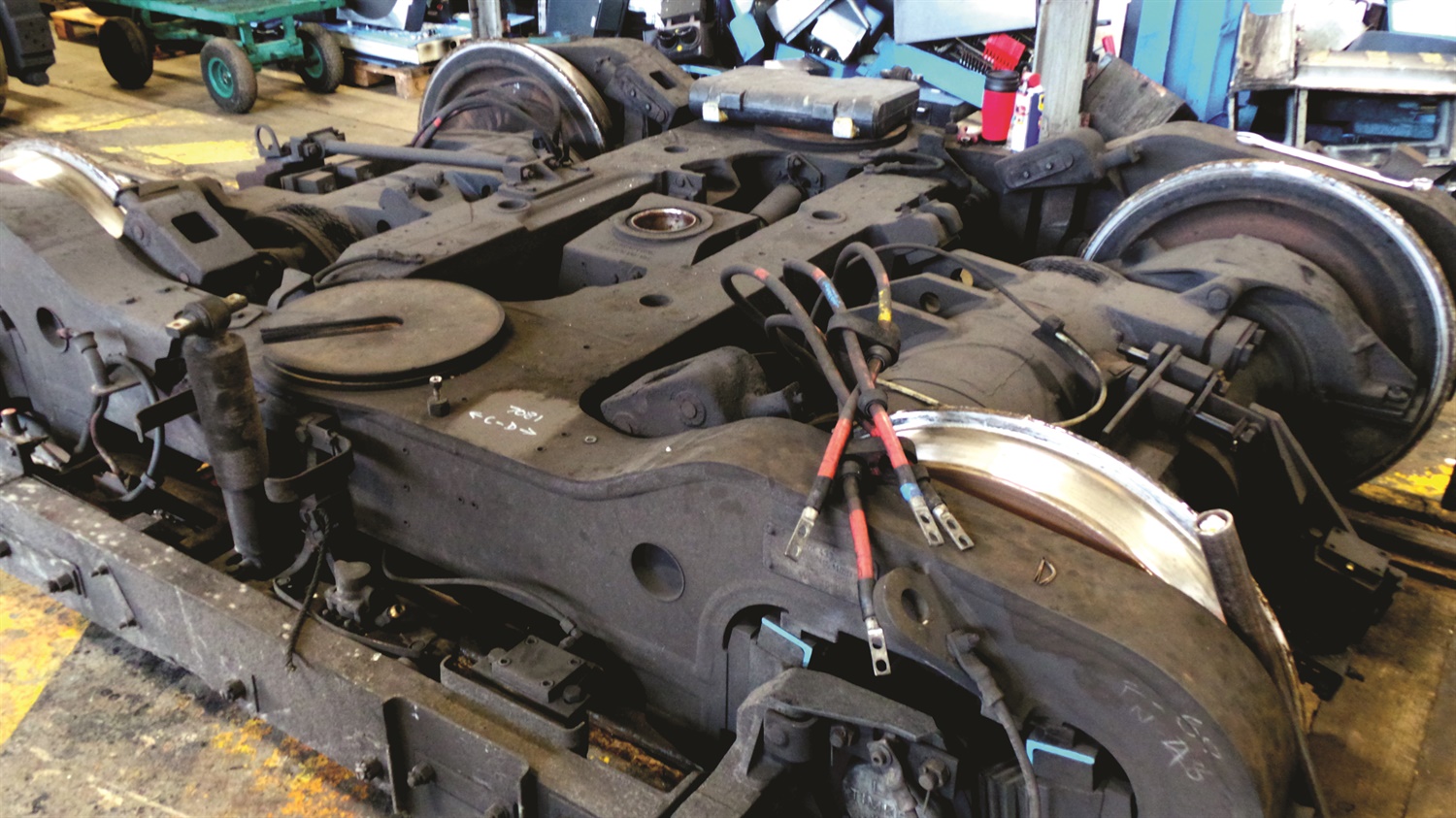
Bogies
The bogies were built by Bombardier 10 years ago and are in “excellent condition”. The original D-Stock bogies were too rigid for their tracks and had to be replaced from 2000-03, replaced with Bombardier bogies (Adtranz, then). The new version, similar to those used on Northern Line stock, had a flexible frame designed to give a good passenger ride on indifferent track.
All of the third and fourth rail equipment has been removed, leaving just the traction motor on each side of the bogie at the moment. Even with the further equipment that still needs to be added, the bogies are expected to be a lot lighter than they were.
The new layout to be installed on the underside of the carriage will be very different from what came before. The fuel tank will be placed in the centre of the undercar, roughly in line with where the London Underground badge appeared on the side of the old stock. Moving from here towards the rear of the car you will find the first genset followed by low voltage and high voltage equipment cases, and then the second genset and main bogie.
To the cab side of the fuel tank will be all of the DC chopper control – the brake reservoir and main air reservoir, equipment for sanders and potentially air con.
Taking me under the carriage, Rowell explained that the body height of the units is being lifted by 73mm to achieve the required gauging. This is being achieved through the use of suspension rubber on the centre pivot and on the vertical dampeners.
“We’re not just doing that, we’re also doing investigations for the VAMPIRE modelling for the bogie, just to make sure that everything in terms of sway is within tolerance,” he added.
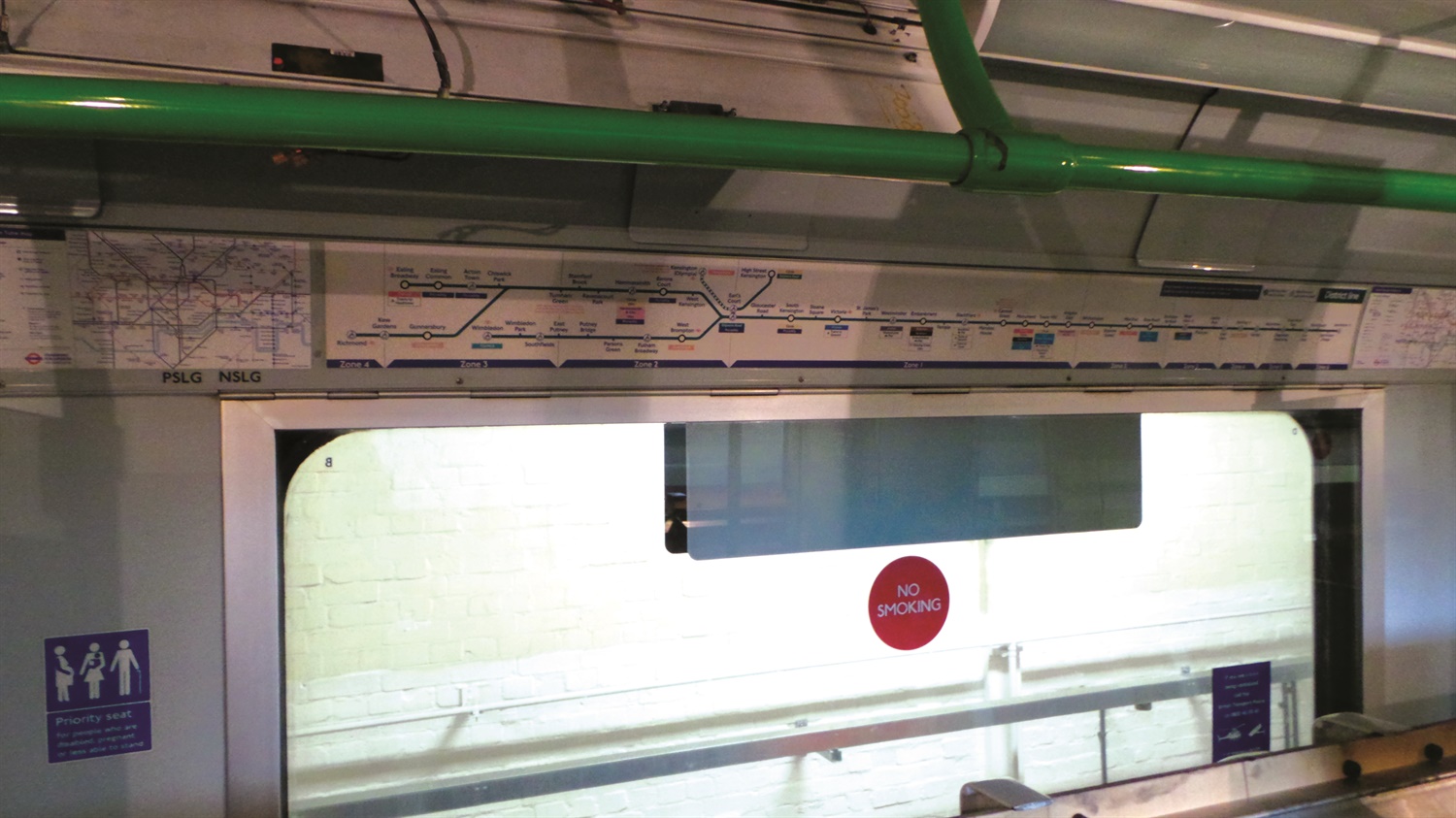
Interiors
The interior of the cab has been completely stripped out. The door at the front-centre is currently still there, but it is set to be removed and replaced by a steel pillar that will be braced into the structure.
The cab desk that will be installed has already been designed and mocked up. It will be set back slightly from its previous position to provide added protection for the driver and feature new controls including CCTV, driver-only operation and a mainline master controller.
Wiring in the cab has all been removed and will be replaced, a decision Rowell said was made “to make sure we’ve given the highest degree of reliability we can”. The carriage interior is currently all bare metal, although an old District Line map could still be spotted in the unit I walked through. Rowell explained that the Passenger Information Systems and CCTV that will be installed will be all new – the previous equipment was mostly from now-defunct suppliers.
The doors will be brought up to specification and some possibly sealed off depending on the layout the TOCs desire. If doors are blocked off, the likelihood is the process will be reversible to give the customer maximum flexibility.
Between carriages, Vivarail plans to have rubberised exterior gangways to allow passengers and staff to move freely.
The current heating unit will remain in the prototype but Rowell said that for production units they are looking at installing a system that utilises heat from the engines. LED lighting is also being installed all the way through the train.
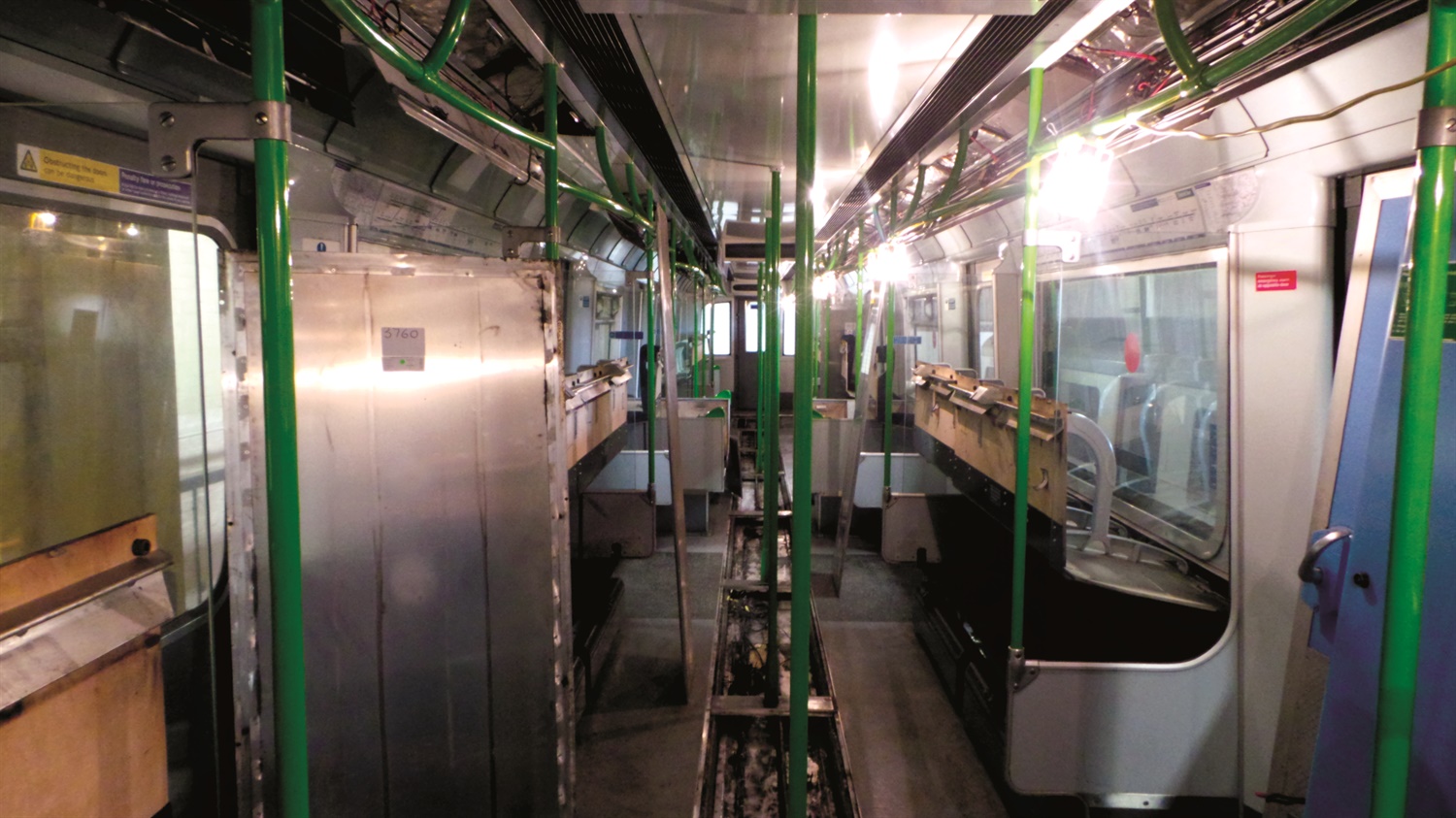
Next steps
That was it for the tour. For an empty shell of a London ‘cast-off’, as its critics call it, the D-Train is much more exciting than it sounds. The reality is that in several months it will be almost a brand new train, with only the bogies and the bodyshell left over from the old units.
Before then, however, Vivarail has a lot of work to do. First up is a crash test where one of the units will be written off to prove the safety aspects. Then at the end of May the prototype’s traction control package needs to be tested and proved, before the media and industry figures stop by in June to see it in action. The company wants the prototype fully certified by September and then the production schedule will begin. From September to November, one carriage will go through production a month, to allow for training and for the final processes to be locked in. If in December the resulting train is certified, the full production line will go into operation, churning out two trains a month. With enough stock to produce 70 three-car sets, production could be completed within three years.
It’s an ambitious schedule for an ambitious project. Rowell knows there are a lot of disbelievers out there, however he remains undaunted.
“Ultimately we’re here to provide an option, we’re here to provide something which is going to be a cost-effective solution. Having myself been in the situation where I’ve been short of rolling stock, the ability to be able to say ‘Right I want two units’ or ‘I want three units’ is fantastic, especially given the fact that there is no rolling stock in the country readily available and there’s not going to be for quite some time. So for myself really, I’m looking forward to the overall output, and hopefully the rail industry will be a better place for it.”
Before walking me out Rowell shows me one final mock-up of the front-end of the D-Train. He points out a little detail that previously had gone unnoticed, and as I leave I realise we may not be calling it the D-Train for much longer, instead we’ll be talking about the Class 230.
Tell us what you think – have your say below or email [email protected]