01.01.15
Understanding the causes of low adhesion
Source: Rail Technology Magazine Dec/Jan 2015
Low adhesion is a major problem for the railways, in terms of performance, safety and cost, but a new research project aims to shed more light on the phenomenon. RTM spoke to Dr Helen Viner, chief scientist at the Transport Research Laboratory (TRL), and Dr David Thompson of Balfour Beatty.
Since August 2014, a South West Trains (SWT) Class 159 has been continuously collecting data using a specially-fitted pair of accelerometers to try to put into practice some previously theoretical approaches to low adhesion monitoring.
TRL, the Transport Research Laboratory, is leading the project with Balfour Beatty Rail and SWT, part-funded by Innovate UK under the ‘Accelerating Innovation in Rail’ programme.
Balfour Beatty Rail had an existing project with SWT to fit its TrueTrak Geometry measurement system to two 159s, as well as some EMUs.
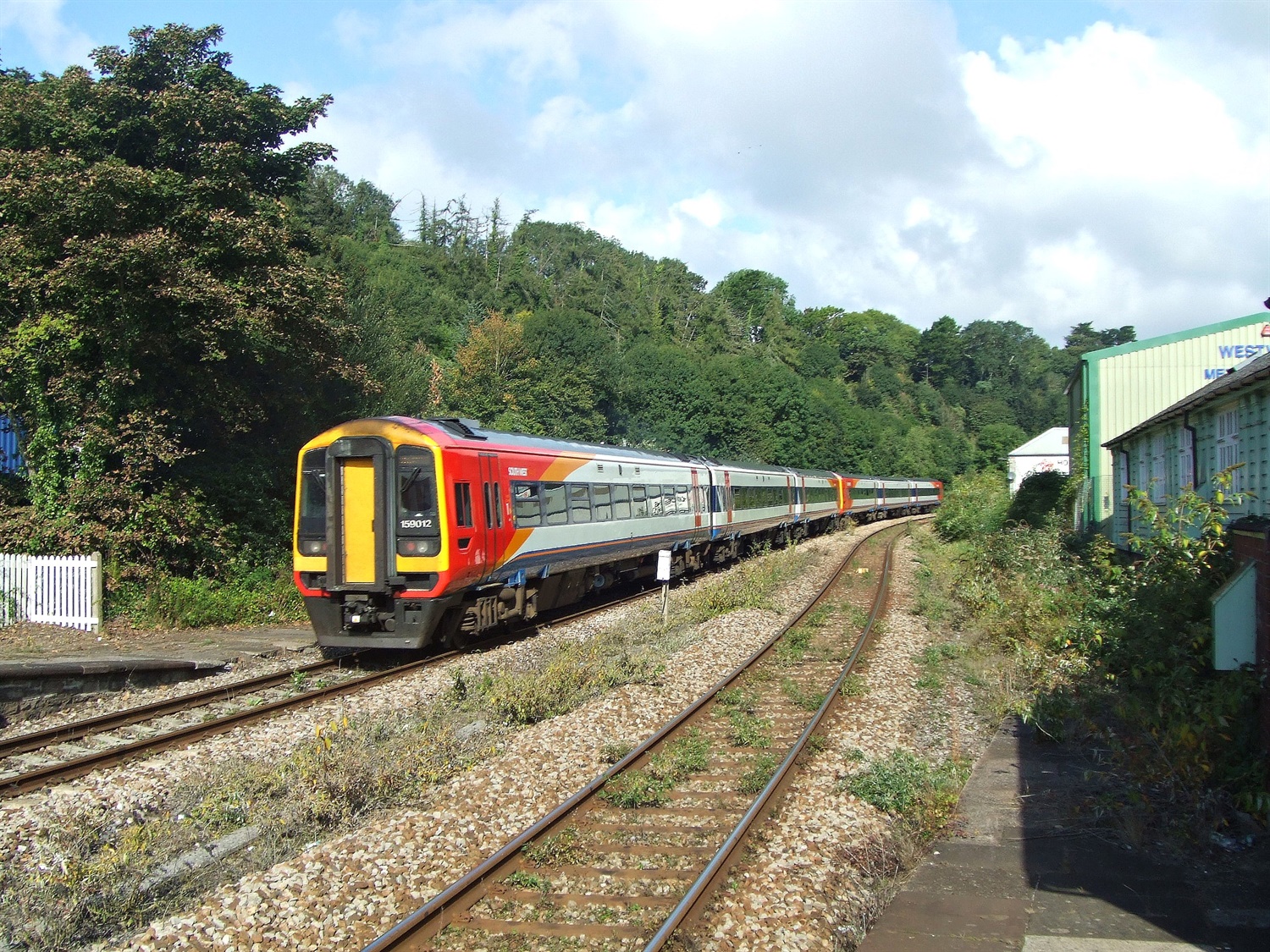
(Photo courtesy Hugh Llewelyn, Creative Commons)
But SWT was happy for TRL to ‘piggyback’ on this project and fit an extra pair of accelerometers to one of the 159s, as part of research into better measurement technology that will enable the phenomenon of low adhesion to be better understood and railhead treatments to be better targeted.
The instrumented train covers about 1,000km per day on its routes from Waterloo to Salisbury, Exeter and Bristol, plus services to Southampton and Portsmouth, during which it generates 3GB of raw data.
TRL analysis is ongoing, and it is too early to say for sure whether the method will prove valid, but chief scientist Dr Helen Viner told RTM: “The first place at which it might have gone wrong was if we hadn’t recorded anything interesting with the accelerometers.
“That’s not the case: we can certainly see from the first results coming through that it’s looking interesting, and we’re getting quite excited about it.
“But we’ve still got work to do before we can say that what we are measuring is linked to adhesion conditions. Having measured throughout the autumn, we’ll be able to look back and compare with forecasts and actual delay-attributions to see whether our measurements link to conditions that were being experienced.”
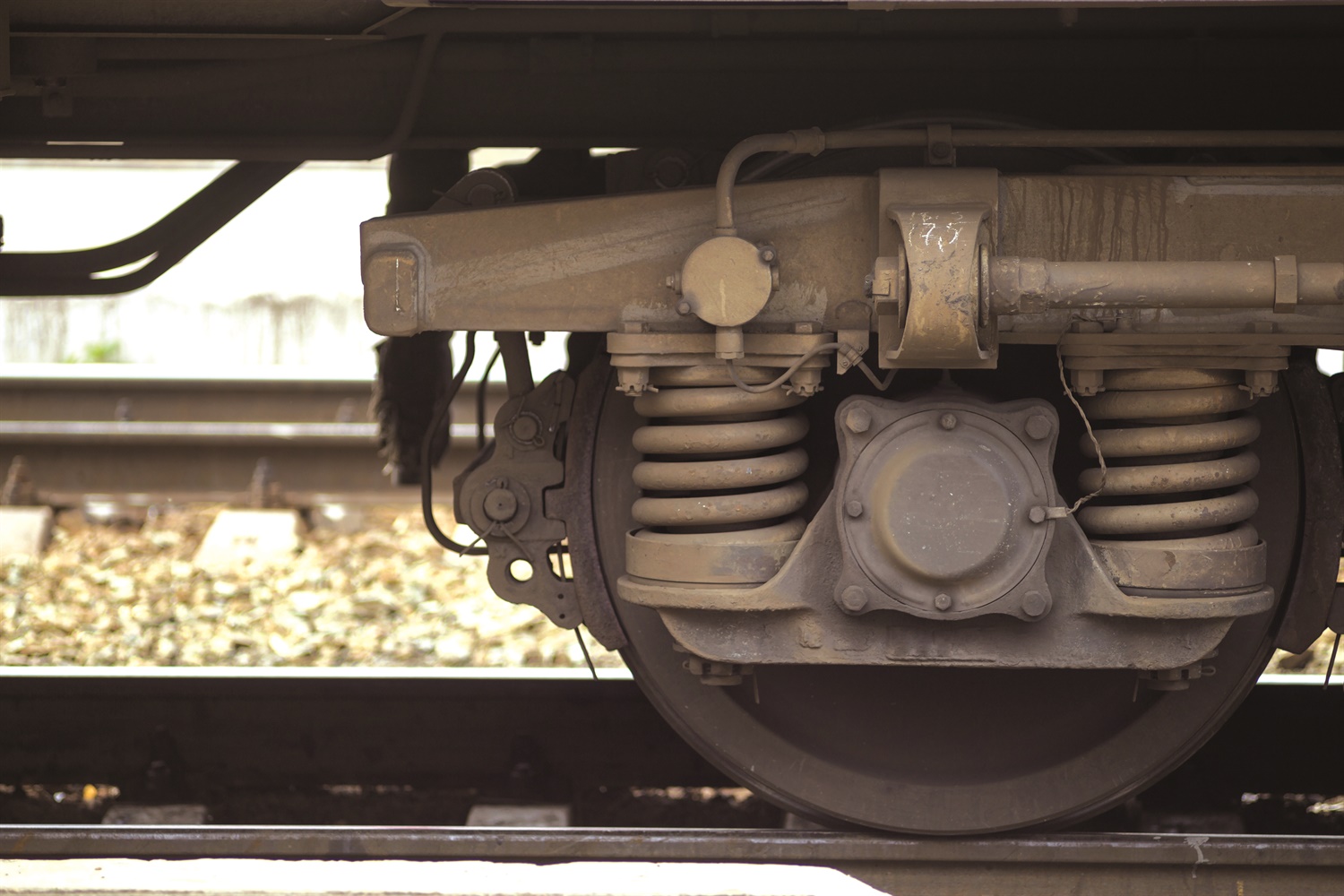
Not just leaf fall
The causes of low adhesion are not comprehensively understood and there are no measurement methods that are suitable for widespread and routine monitoring of adhesion conditions. Although associated with leaf fall, adhesion problems can be experienced throughout the year.
The new project builds on RSSB-funded modelling by Loughborough University suggesting the accelerations experienced by wheelsets and bogies are indicative of local adhesion conditions. Dr Christopher Ward led on this work.
Dr Viner explained: “We’re looking to use some of their findings as the basis of our measurements.
“The train operators are more organised about the treatments they apply, but the trouble is that the phenomenon of low adhesion is not very well understood. We do a lot of work with skid resistance on the road network, measurement of which is very routine; if we had a similar system on the railways capable of being used routinely, then at the minimum we’d build up a better pattern of where the problems were and when they were likely to happen. Ideally, if it was capable of working in real-time, and fitted to a high proportion of rolling stock, then you’d be able to react to conditions in real-time.
“As far as I know, this is the first time anybody has tried to put this approach into practice for detecting adhesion conditions. This was the ideal opportunity, and the accelerometers are now generating an absolutely vast amount of data,” Viner said.
“We’re hoping that by March/April, we’ll be able to go back to SWT, explain what the data is telling us, and work with them and other interested industry partners to see how we take it forward another step.”
That could include better targeting of railhead treatment, but also potentially incorporating adhesion data into operators’ Driver Advisory Systems. “That would need the data analysis to be in real-time, so would certainly be some way into the future,” Viner said. “The first stage would probably be a more targeted research programme, where we try to understand the phenomena better, before moving – if we can get it working – into real-time monitoring, providing real-time feedback and operational data.”
Track geometry monitoring
Dr David Thompson at Balfour Beatty’s Engineering & Technology Solutions business explained that the TrueTrak analysis engine, the hardware for which can be either body-mounted or bogie-mounted, is already fitted on all bar one of Network Rail’s track recording vehicles. It’s now “the routine track geometry monitoring kit for the UK”, he said. Fitting it to passenger service vehicles is still comparatively rare in this country, though some new fleets are being built with the systems pre-installed, such as the IEP fleets for Hitachi. The idea is to get unattended track geometry monitoring to supplement the less-frequent audit runs by Network Rail’s official yellow measurement trains. “This work with SWT enables a two to three times a day level of track geometry data collection,” he said. “The more data you have, the easier it is to plot trends and quickly identify faults.”
He worked with TRL to supplement the main track geometry monitoring system with the new sensors, and said: “It’s an interesting project, and I see it as a very useful add-on.
“If it can be done simply by adding a couple of additional accelerometers – with the rest done in software – then it’s a fairly easy win for anyone who already has a geometry system.”
Tell us what you think – have your say below or email [email protected]