23.12.15
Soil mechanics
Source: RTM Dec/Jan 16
Sorting out the Harbury Cutting once and for all has been a mammoth task, interrupted by a severe landslip in early 2015 that forced a line closure. But with the work now all but finished, RTM caught up with Network Rail’s route asset manager Tony Butler, senior asset engineer Luke Swain, and site engineer Joe Allen from contractor J Murphy & Sons.
The main remediation works at Harbury Cutting are now complete, bar some final clean-up operations going on until mid-February.
Following a small slip in early 2014 and a much larger and more disruptive landslip in January 2015 – while engineers were still on site to see it happen, though no-one was hurt – Network Rail decided that drastic reprofiling of the cutting was needed.
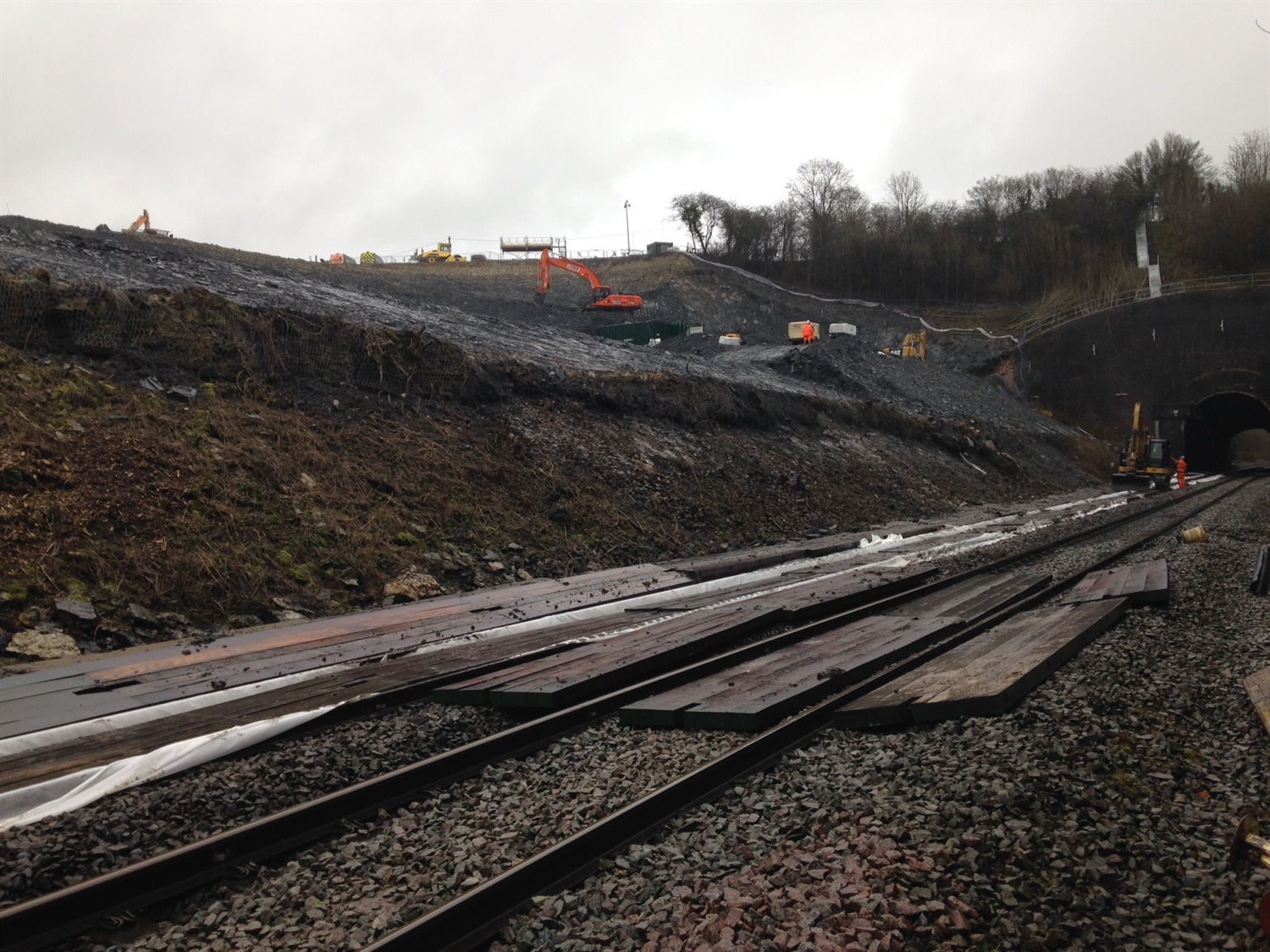
This meant a regrade not 5m from the track, as originally planned, but 35m away – behind the faultline thought to have caused the main slip, when water effectively built up behind it. The fault zone was a band of clay between 3m and 5m thick, softer and less permeable than the Rugby Limestone on either side. Torrential rain caused so much water to build up ‘behind’ the faultline that its weight and pressure eventually caused the whole slope to slip.
During that slip, 326,000 tonnes of soil, some 160 linear metres wide, moved forward 26 metres in one hour. Although it did not bury the track, it was serious enough to require the temporary closure of the line between Banbury and Leamington Spa while emergency works took place.

Initial emergency and long-term resilience
Thanks to a good plan, plenty of collaboration and 24-hour working, the cutting was made safe enough for the line to reopen by mid-March, three weeks earlier than first expected. But those emergency works were then followed by months of civil engineering – or, more specifically, muck-shifting – to deal conclusively with the geotechnical problems at the site.
Site engineer Joe Allen from J Murphy & Sons, the main contractor, said: “The designers thought the best thing to do in this case was to remove any risk from the fault, so we dug everything back to behind the faultline.”
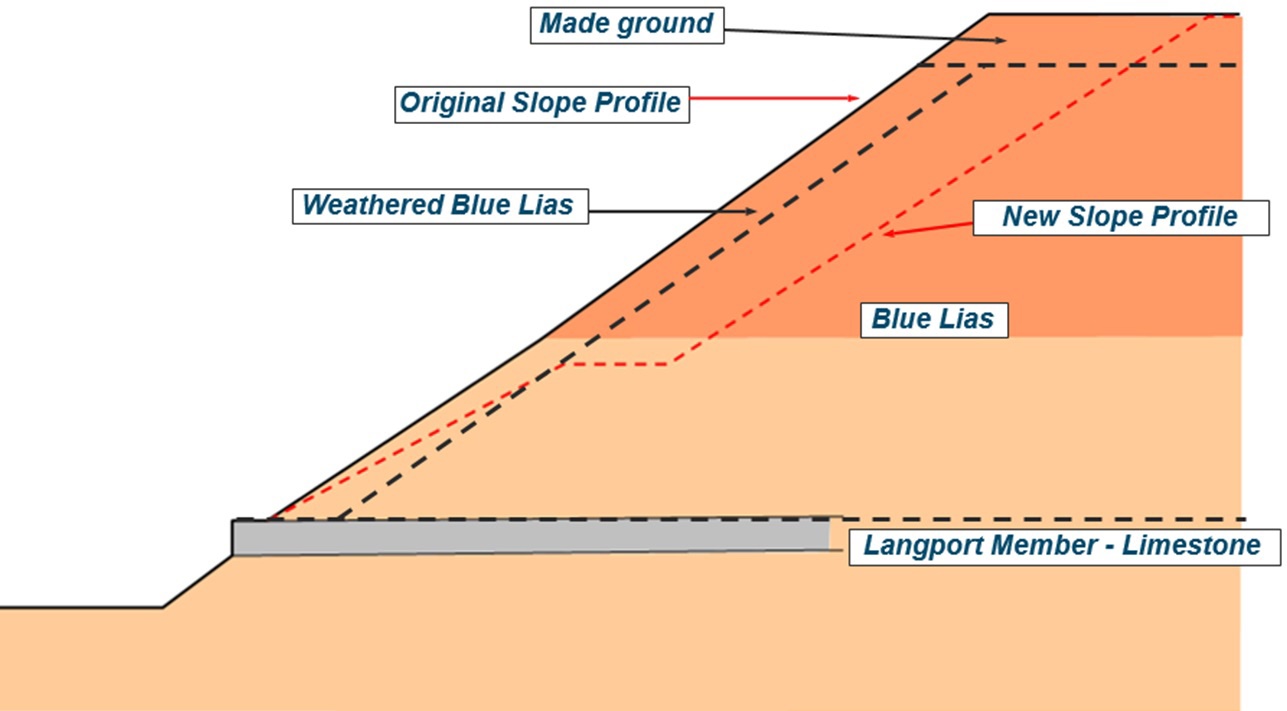
Two 1:2 slopes were created, both 15m high with a berm between them and a 1:3 shoulder along the top batter, all with a huge amount of drainage.
Allen and other members of the Murphy team were already on site in 2014, doing smaller-scale remedial works following the smaller slip that year. It was Allen’s first job with Murphy, and he joked that he came to Harbury for two days in October 2014 “for a look around”, but then never left.
Even while the original set of remedial works were taking place, tension cracks had been spotted and a full monitoring system of pegs and inclinometers was in place, allowing engineers to see accurate data as the faults worsened.
Network Rail’s route asset manager Tony Butler told us: “To do successful remedial works, you need to know what caused the failure – identify the root cause and then treat it. We realised early on that the scale, size and complexity of Harbury meant that we could be there debating for quite awhile over the exact cause, and why such a large landslip then developed.
“Early on, we got a very broad group of consultants in, by the first week. We had people there from four or five companies, with 20-30 years plus of geotechnical experience. We also brought people in from outside the railways, such as Schlumberger [a giant engineering company primarily involved in the oil and gas sector], which was involved due to Mark Carne’s involvement as well.”

Worst-case scenario
Initial ideas on what caused the slip came quickly but it was still not certain after those first few days. Even now, there are “still three or four theories, depending on how you look at the data”, Butler said. With insurance companies and loss adjustors still involved, there was only so much he could say on that topic, but some of the disagreement came down to whether it was analysed as a soil mechanics issue or as a rock mechanics issue.
He explained: “We had to make sure the works we did took account of the worst-case scenario, in terms of what that potential failure driver could be. That is why we have ended up with a very large-scale remediation.
“It became fairly obvious early on that the only way we could sensibly treat it was as a giant muck-shift operation.”
Many companies were involved with the ideas, design and reviews, including Tony Gee & Partners, Atkins, Murphy, RJM Ground Solutions and others.
“The actual design we ended up with was a combination of a lot of people’s input,” Butler said. Even though there are disagreements on the precise cause of the slip, “everyone agrees that the work that has been done should be enough” to prevent anything like it happening again.
Getting the right team in place
Network Rail and Murphy were both frank enough to admit that once the nature of the job changed, there were questions at first about whether the company – one of Network Rail’s top 20 suppliers, winning £155m of work for it in 2014-15 – was the right choice.
Butler said: “Once we decided on what was going to be done – and we did decide, probably within 48 hours or so, that this was going to turn into a muck-shift – the question was, is this one of Murphy’s strengths? Because they’re a civil engineering constructor, and this was almost turning into the kind of thing you’d expect to see at an open-cast site or a quarry site.
“But Murphy demonstrated fairly quickly, by the amount of plant and personnel they got shifted to site quickly, that it was something they could do.”
He said his team have had good professional and personal relationships with Murphy personnel for years, but even so they were “pleasantly surprised” at how proactive the company was. “They weren’t passive at all, sitting there waiting to be instructed. They very much worked with us and said, ‘what are you thinking, we’re thinking this, this is what we can do’. It was a case of working together, and [asking]: ‘What do we have to do to get the railway open?’”
Allen echoed this, saying Network Rail started out “a bit apprehensive”, wanting to ensure Murphy could fulfil the job. “But, definitely, once they saw how we mobilised in the first two or three days, and during the emergency – plus the support, the health and safety aspects, and the management of it all – they were very impressed. The route delivery director, Karl Budge, complimented us a number of times.”
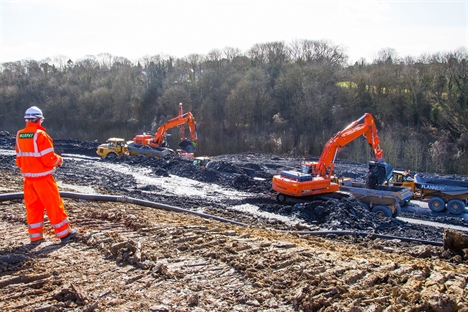
Handling the weather
Heavy rain was one of the proximate causes of the landslip, and the weather continued to be an issue afterwards, costing at least a few days of work.
But it could have been even worse without efforts by Murphy to keep the access and slopes useable, for both those working on foot and driving machines. Key to this was bulldozing slopes whenever there was rain, sloughing off the top slippery layer and exposing a fresh layer (allowing more traction) below.
Butler said: “They made sure that in wet weather conditions this would regularly be done so the site didn’t get bogged down. It was little things like that that enabled them to keep up.”
Even this wasn’t always enough, Allen said, describing the scene after some bouts of heavy rain as “absolutely horrific…you don’t sink in it, you slide, which makes it extremely dangerous”. He added: “The Harbury Blue Lias mudstone is very unforgiving.”
But when conditions were good and the muck-shift process was in full flight, it was “amazing” to see, according to senior asset engineer for Network Rail, Luke Swain.
Butler added: “When we first started down there doing the muck-shift, it was going to be a fairly simple equation: how much muck could you shift in a day and what would get us to where the railway was open. Initially, we were hoping to shift 8,000 or 9,000 tonnes a day. We eventually got it up to almost 20,000 tonnes.”
In total, more than 580,000 tonnes have been excavated. Most of this was initially ‘stockpiled’ nearby for subsequent removal to cap off a local landfill site.
All hands on deck
When RTM spoke to Allen in late 2015, there were still about 20 workers on site and about 10 machines, half doing the muck-away and half involved with other finishing works.

This was a far cry from the situation during the ‘emergency’, as those involved universally term it, when 24-hour working was necessary and the site was a hive of activity. There were two rigs working on the soil nailing at all times, done in conjunction between Murphy and Vertical Access Ltd, with 180 soil nails each installed 20m deep. A de-watering well was drilled at the crest.

During the peak, there were 50 machines and 60 staff on site, who had to live close to the site – much like those who dug the cutting by hand in the late 1840s to accommodate the Oxford to Birmingham GWR Line. It was, at the time, the largest man-made cutting in the world – and despite the involvement of Brunel, has suffered from landslips virtually since it was built.
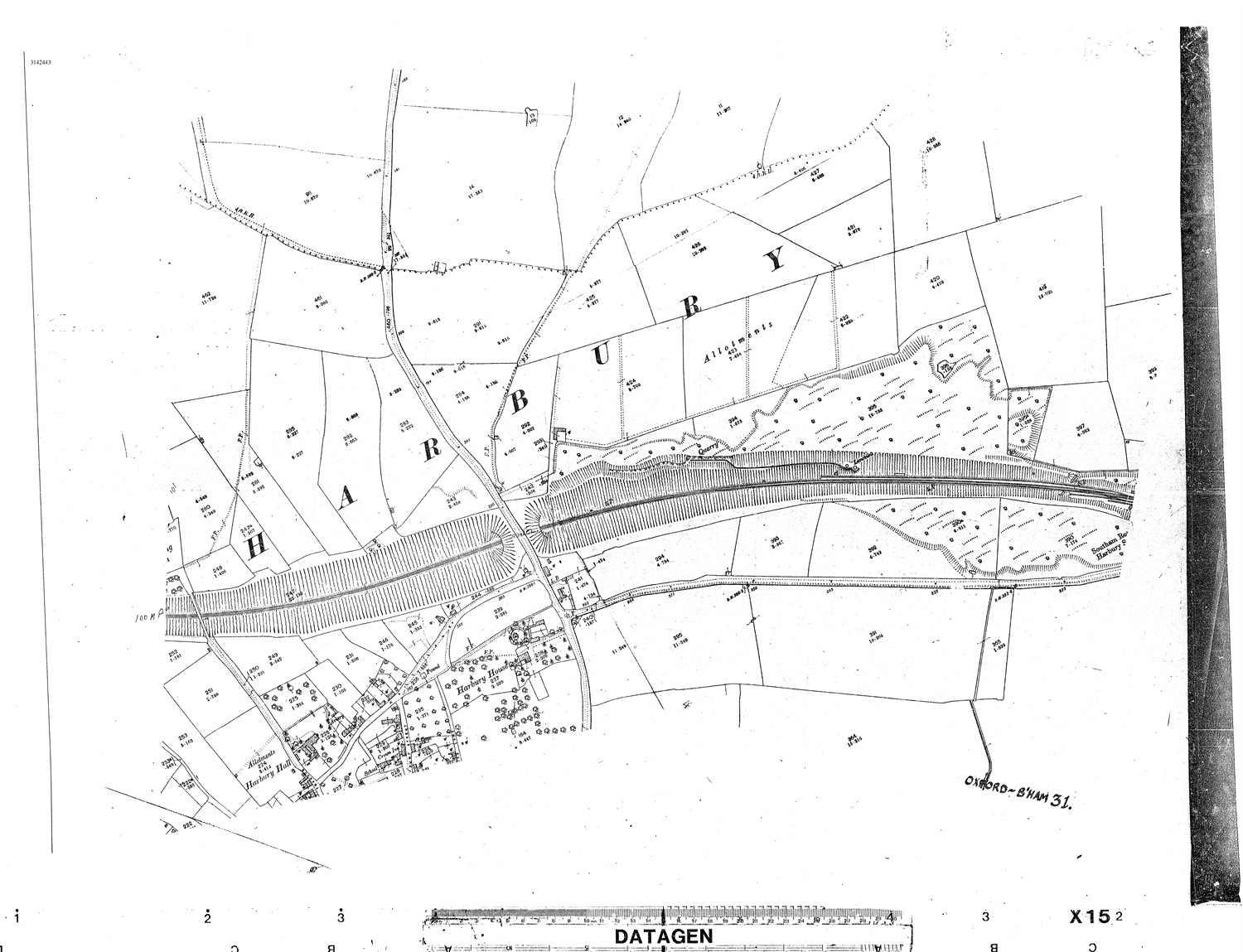
Extending the site
As part of the long-term remediation plans for the slope, and to make use of the fully mobilised team on site, Network Rail decided to extend the reprofiling an extra 200m westwards, far past the area of the actual failures near the 67m-long tunnel under Deppers Hill.
Swain said: “That was done under the original remit, but at that end we were only going to improve the existing drainage. We only had to do the major scheme there because of this mass of material that had moved near to the tunnel, which left almost a void in the ground for more movement of soil and rock from the other end of the site. You either fixed half the site and lived with the risk of another major failure, or you just deal with the problem there and then – and that was the decision that was taken.”
After the emergency, the 24-hour shifts became 12-hour daytime shifts, with track possessions every Saturday night to upgrade the cess drainage. There were constant surveys to ensure “we weren’t just moving the flooding problem from up on the hill down to the track”, Allen said.
Data and monitoring
There has been lots of manual and remote monitoring before, during and after the emergency, using monitoring pegs, piezometers and inclinometers, plus a drone to carry out sophisticated imaging.

The remote monitoring does remain on the lower slope, where any movement could suggest a risk to the track.
Swain said: “But as we’ve gone through the project, and by implementing the design, we’re reducing the risk to track, and we’re being left with a Eurocode 7 compliant design on the slope.
“We will be undertaking a number of boreholes, using an array agreed with Coffey Geotechnics, the contractors and the designers, and we’re going to be going out there and installing inclinometers and piezometers into those boreholes. So, going forward, we’ll continue to manage the earthwork via our regular monitoring programme as we do at a number of sites.
“The decision has been taken not to remotely monitor it, because obviously in that section we’ve significantly reduced the risk now. We’ll be doing manual monitoring on a monthly basis, or a two-weekly basis when we first install the equipment.
“But while it’s a construction site, we’ve had 24-7 watchmen. That’s only just stopped. We’re at a stage now where the risk is reduced enough that we don’t need that.”

Community work
Harbury itself is a small parish of only about 2,500 people, and the contractors did their best not to disrupt their lives more than necessary. During the 24-hour working period and the emergency, there was noise at night, and some villagers raised concerns about the stability of the opposite slope, where there are more properties.
Allen said: “We’ve more or less embraced the community as much as we could. We’ve donated building materials to the local hall, we’ve resurfaced a car park, and we’ve also organised tours for the schoolchildren – we had about 150 schoolchildren over a period of three days who visited the site. They got a demonstration of the machines and learnt about safety and exclusion zones, and got a lucky bag. The Women’s Institute visited a number of times. We want to be engaging the community, getting Network Rail out to meet them – to show them that we’re not just digging here for the fun of it.”
The top of the cutting was seeded to return it to grassland, and protective measures were installed to safeguard wildlife, including great crested newts, butterflies, bats and badgers.
Safety and workflow
Safety has been exemplary on the site, with no reported accidents or incidents despite hundreds of thousands of hours worked.
Allen said: “There was a safety manager based on site from the start. With it being a changing site, with a huge amount of plant movement, the risks and hazards are being created and closed off every day. It was a challenge to keep everything under control, because while everyone had the end in sight, safety was a big part of that too – there was no point in doing it with something going wrong in the middle. So there was a massive emphasis on safety.
Swain added: “It’s been a well-run project from that perspective.”
The muck-shift workflow was also well-managed, Butler said, with a one-way traffic system and processes that ensured machines and plant weren’t left idle. Allen said: “We basically split the site. There was the ‘goods in and out’, including the muck, and then the internal site movement. We put a foreman in charge of the muck-away, a supervisor to look after all that, and kept it separate from the general site.”
That, plus GPS machine control, freed up time for the engineers to concentrate on other tasks, he said.
‘The best team possible’
Butler said: “They [Murphy] told us they brought in their ‘A team’. They cherry-picked the best machine operators and site operatives from the rest of their sites to make sure that we got the best team possible on this to get the railway open as soon as possible.”

Allen added: “Everyone just pulled together, and everything we wanted, we got. We also had the designers based on site, which was a big benefit during the emergency. There was no emailing, you could just go in and ask them questions.
“It was a big team effort between people in the ground and in the office. Harbury was pushed to the top of table. With jobs of this scale, you really need a good team behind you, and a good core back-up team.”
That message was echoed by Butler, who told us: “On a company level, it demonstrated how well we can work in a crisis – a bit like Dawlish. If there is something big and ugly that happens, the relationships we have within [Network Rail] and externally allow us to deal with it fairly quickly. There doesn’t tend to be much navel-gazing, or waiting for other people to take the lead.
“It was great to be working in an environment where everyone was focused on the goal of ‘what do we need to do to make this happen’. That’s the key lesson: if you’ve got the technical guys, let them get on with the technical stuff, let others handle the business and liaison end. It worked really well, and the lack of interference was excellent. When you’ve got a good team, you can let people get on with it.”
Tell us what you think – have your say below or email [email protected]