17.12.14
New monitoring system to reduce Victoria Line delays
A new remote monitoring system, NI CompactRIO, is expected to reduce lost passenger hours on the Victoria Line by 39,000 per year by detecting potential track circuit failures before they occur.
Designed for London Underground (LU), the new system will allow the operator to better understand a critical asset, learn the behaviour of a faulty track circuit, identify those that could potentially fail and alert maintenance prior to this event occurring.
Over the past eight years, £1bn has been spent upgrading the Victoria Line’s rolling stock and signalling and control systems to raise capacity to 33 trains per hour.
The new signalling system uses 385 jointless track circuits (JTCs) to detect train position, maintain safe train separation and deliver train headways capable of meeting an extremely demanding timetable. However, no provision was made for any condition monitoring of track circuits, which play a critical role in the safe and reliable operation of the railway, during the design and installation.
Sam Etchell, testing and commissioning manager at LU, said: “Due to the critical nature of the asset, a failed track circuit has a major impact on the service and constitutes the biggest cause of passenger disbenefit on the Victoria Line, amounting to £1.5m since their introduction.”
The Victoria Line ‘Condition Monitoring Team’ – six professional engineers with rail, software, electrical, mechanical, network and engineering backgrounds – delivered the new solution. National Instruments’ Silver Alliance Partner, Simplicity AI, supported the project by providing additional software consulting services, and the new the system was introduced onto an operational railway within one year of the concept design.
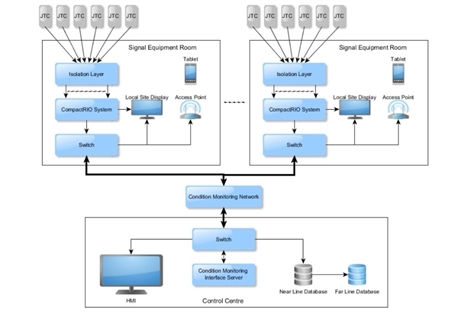
The scope of the project consisted of designing, integrating and installing an intelligent remote condition monitoring system that could perform real-time analysis of voltage and frequency for all 385 JTCs across 45km of deep tube railway to predict and prevent failures and subsequent loss of passenger service.
It has resulted in a central condition monitoring server that processes a live 10Hz data stream from every CompactRIO device, which totals more than 7,000 data samples per second. The system compares each received frame of data to a defined standard frequency and voltage so the server can make an independent decision on the health of each track circuit. In addition, the server stores all of the data in a near line and far line database architecture so that long-term trends on large datasets can be analysed.
The central server can push asset condition alerts to a human machine interface (HMI). The HMI is a large touch-screen device that displays an accurate scaled replica of the Victoria Line track circuit configuration.
There is a plan to deploy two HMIs for faster response times – one in the Victoria Line control centre and another in the maintenance control centre, both of which will be used by signalling maintenance staff.
Rahman Jamal, technical and marketing director for NI in Europe, said the accuracy, reliability and flexibility of NI hardware and software was a crucial factor in the development of an innovative system to reduce lost customer hours on the Victoria Line.
Alongside the HMI, a suite of touch screen devices can display the data in the line-side equipment rooms and through a smartphone or tablet. This means the data from the CompactRIO devices is available anywhere on the Victoria Line through a connection to the new condition monitoring network.
“Connectivity is vital as we move into the age of the ‘Internet of Things’. In this case, we wanted to ensure that the monitoring data would be accessible on the mobile devices that we all carry with us today,” said Jamal.
This news comes as it was revealed that last week the LU network carried a record 28.346 million people. This exceeded the last record-breaking total reached in the week ending Saturday 13 August 2012 during the London 2012 Games when 28.235 million journeys were made.
Tell us what you think – have your say below, or email us directly at [email protected]