01.01.13
Next steps at Central Rivers
Source: Rail Technology Magazine Dec/Jan 2013
Adam Newton, Bombardier’s general manager at Central Rivers Depot, speaks to RTM about effective, sustainable maintenance that stems from great working relationships.
Sometimes good service is not down to the introduction of radical new technology, but continuous improvement to working practices and good use of data. RTM spoke to Bombardier’s general manager at Central Rivers Depot in Burton-on-Trent, Staffordshire, Adam Newton, about its contract extension with Virgin, condition-based maintenance and innovation that fi ts short time scales.
Bombardier Transportation has been awarded an extension of its fleet maintenance contract with Virgin Trains until 2016, following Virgin’s own 23-month franchise extension on the WCML to 2014.
The £106m contract will see maintenance provided for the Super Voyager trains in operation on the West Coast Main Line.
The trains will be maintained at Central Rivers Depot, and at other outstations across the network. The depot, built specifi cally to maintain the Voyager and Super Voyager fl eet and opened in 2001, employs 360 people.
It is a central hub for maintenance datagathering and the use of diagnostic technology to identify issues before they affect passenger services.
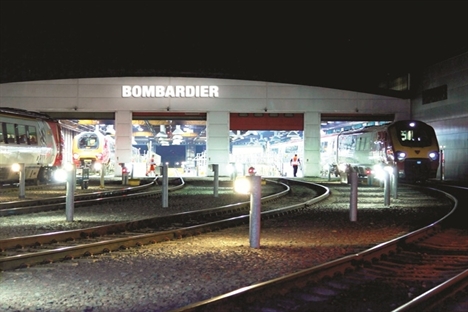
A ‘great shop window’
Newton welcomed the maintenance contract extension and said: “There’s several really strong aspects for us; the fi rst is a guaranteed revenue stream until March 2016, which gives us the stability to keep doing the right thing, for Virgin, for the Voyager product and of course for our people as well. That’s really positive for us.
“Virgin is a high-profi le customer. We’ve been working for them for 13 years, so a lot of mutual trust and respect has been won over that time. This is an opportunity to continue that.”
The fact that Virgin’s 21 Class 221 Super Voyagers are in operation on WCML helps Bombardier to maintain a “really strong position in the services market”, Newton said. “West Coast is considered to be one of the busiest and arguably the highest profile franchise, so it’s a great shop window for us. Operationally if you work on a franchise with Virgin on West Coast it can make a real difference.”
The other 23 Super Voyagers, and the 34 Class 220 Voyagers, are operated by CrossCountry.
Future optimisations
Newton said there were a number of optimisations under discussion for the extension.
He said: “The risk of a short extension such as this is perhaps – in a more traditional view in the industry, or with a less mature partnership in place – that it could lead to a bit of stagnation. But we try to keep ourselves committed to doing the right thing.
“One area we’re going to work together on is to reduce the fuel consumption of the vehicles. It’s a very obvious thing, with a positive impact on cost but also a strong sustainability argument there.
“If you could get to the point where the trains are at the ‘next step’ in terms of fuel effi ciency, which we think we can, it gives us different options in terms of diagrams.
“They’ve got some technology enhancements that are possible, but experience shows that if we act on quality and timely data, which is what we’re all about, we can provide reliability and can get operational costs down. Ultimately, that’s the goal.”
Fundamental reliability
Discussing the merits of new technological innovations versus improved working practices, he explained that continuous development of working relationships is the most important factor in running a successful maintenance programme.
“If you get the fundamental reliability right, which we have done over a number of years, it can make a difference.”
He added that it was important “not to think that a big technological modifi cation on the train is some kind of magic button”. He said: “If you’ve got good data, good people, and you work on that together, you can do great things with the product. I think that has been very successful so far.”
These factors can deliver long-lasting sustainable benefi ts and reduce the risk associated with major change in a relatively short extension.
The cornerstone of maintenance
Discussing whether it was more important to work on preventative maintenance or to develop quick and effective reactions to disruptions, Newton said: “Preventative maintenance has got to be the cornerstone of any fl eet obviously, it’s got to be the driver. But you’ve got to make sure it’s dynamic, so that you don’t stagnate and do the same thing over and over.”
This involves constant optimisation on VMIs (Vehicle Maintenance Instruction) and preventative maintenance practices. Permanent staff are also spread across the network to provide reaction where necessary, as quickly as possible.
Newton acknowledged that good maintenance “obviously reduces the need for reaction” and highlighted the very low impact minutes on the network with Virgin. However, he suggested that the real target should be condition-based maintenance (CBM), with new vehicles having more and more inbuilt capability to monitor their own systems. This doesn’t just apply to the latest models, but could be achieved today with existing rolling stock, he added.
“We shouldn’t assume we can’t get there with a more mature product like Voyager. We’ve got various initiatives like ORBITA, and with improved data we’re in much better shape to target condition-based maintenance.”
Condition-based maintenance
Bombardier conducts regular cycles of maintenance optimisation, analysing data to identify potential improvements.
A recent review found that measuring and checking consumables in the traditional numbers of hours and miles that have gone by could be replaced by checks that take into account a wider range of factors that capture the full condition of the train. This data can then be represented via a simple traffic lights system of need, which can easily be interpreted and acted upon by staff.
There is increasing opportunity to build condition-based maintenance into new vehicles, Newton said, and there are currently pockets of the practice across the railway network. He added: “It’s something that we’re particularly well-placed to take advantage of on this fairly mature product. We’re working hard on making sure we’re really capturing the data about what’s going on.
“It doesn’t always mean there’s a need for a very high-technology, high-complexity solution. Sometimes it can be as simple as just checking certain things more quickly. Our operators now have handhelds while line-side, giving them the capability to capture more data, look more frequently at a lot of things and build up a picture that allows you to make better decisions.”
This new approach to maintenance can provide significant cost savings, and remove constraints on where and when fuelling takes place, offering a wider range of options for timetabling.
West Coast chaos?
Commenting on the recent disruption over the West Coast franchise award, Newton said that the confusion had not signifi cantly affected Bombardier, and had in fact resulted in “quite a success story, at least for us”.
He explained: “It was apparent that the DfT had a problem, but we tried to be really constructive when it came to negotiating this interim service contract. With a good pragmatic and experienced workforce, we’ve got good relations with all the right people and I’m pleased to say that we managed to keep our heads up.”
Newton called the decision to extend Virgin’s contract for 23 months before the start of a new, longer-term franchise on the route “a sensible outcome” and added that clear communication with the workforce had helped to mitigate the impact on Bombardier.
Tell us what you think – have your say below, or email us directly at [email protected]
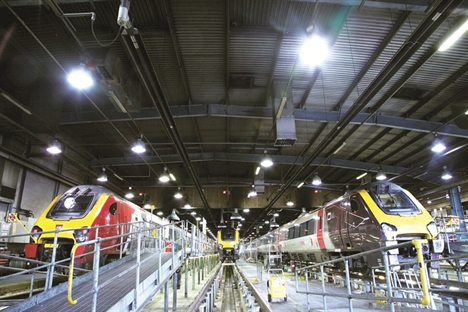