11.09.17
Elizabeth Line rolling stock: a culture of co-operation
Source: RTM Aug/Sep 17
With the Elizabeth Line tantalisingly close to completion and the first of its new rolling stock already on track, David Sherrin, senior project manager for rolling stock at TfL, updates RTM’s Josh Mines on the progress and delivery of the new trains.
There are few projects that have been as eagerly anticipated as the roll-out of Crossrail’s new trains on the Elizabeth Line. Though the project is yet to be fully complete, the shiny Bombardier rolling stock is already out on track for passengers, running on the east side of the line, between Shenfield and London’s Liverpool Street station.
David Sherrin, project manager for rolling stock at TfL, told RTM, the introduction of the new fleet is now in full flow and progressing well.
“We currently have units 5, 6, 7, 8 and 10 in London, and units 5, 7, and 8 are now in passenger service,” he said. “The other two are supporting driver training. Another one came down at the start of August, and then we get to work rolling out the shorter units.
“The stage 1 services from Liverpool Street and Shenfield, which started in June and carries on until stage 3, consist of seven carriages and are 160m long. This is to accommodate the existing Liverpool Street station platform lengths.
“We have the shorter reduced length units which are being delivered. Those are being delivered now, and by the end of the year we will have 11 of those in service, which will displace more than half of the 315s that are in service at the moment.”
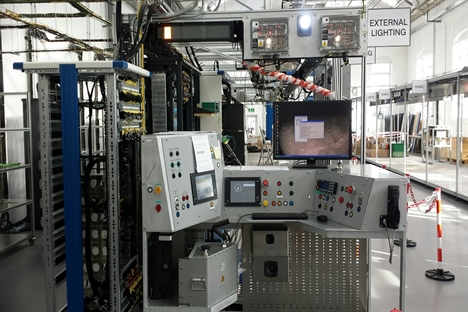
Early teething problems
However, this process has not been difficulty-free. For instance, TfL pushed the introduction of the rolling stock back from May to the end of June. But Sherrin explained that this delay was key to maintaining passenger confidence in the new fleet.
“Stage 1 is really important in terms of making sure we get the trains reliable and understood,” he said. “Crossrail has a staged build-up of services, and the whole idea behind that is to progressively introduce services so we can make sure we keep them reliable, so overnight we don’t suddenly have 65 trains trying to run on Crossrail.
“Crucially, new train introduction is all about confidence. Confidence with our passengers, confidence with our train crew and confidence with the operators. It was really important that we held back for a couple of weeks just to make sure we had settled the units down and that they were going to work.”
To reassure passengers, Sherrin also revealed that aboard every train is a technician to make sure problems can be resolved quickly, and so that any issues are also reported back to base and used to learn and improve the technology further. Besides some early problems with doors not shutting, the TfL project manager stated that the response from drivers and the general public has been overwhelmingly positive.
“The drivers like the layout of the cab. They can see all the indicators, they have two screens giving them indicators of how the train is performing and they also like the forward view they get through the big windscreen,” Sherrin added. “We’ve had great feedback from passengers too. They like that they are air-conditioned and that they’re a lot quieter – on the older trains you were rattling along, but the new ones are quiet and smooth.”
Early bugs in train testing and ‘train zero’
There were some other, more peculiar, difficulties that the train manufacturer encountered during early testing. In particular, despite being tested in an Arctic facility in Vienna and being capable of running in extreme weather, tests back in London found that the windscreen wipers on the trains were not strong enough to clear insects from the front of the train.
“We had tested the wipers in wind, snow, rain and ice, but not with bugs — and we had great difficulty getting the bugs off the screen,” Sherrin explained.
“To fix the problem, we changed the software of how the windscreen wiper works and the amount of force it uses to sweep across. When you have a dry windscreen you need a lot of force to push the blade across, whereas when there’s snow and rain and ice on the windscreen, it doesn’t need as much force.”
Another part of the roll-out process for the Crossrail trains revolved around the interesting and high-tech way the trains were tested at Bombardier’s facility in Derby, using the ‘train zero’ system.
“Bombardier has all the systems on the train, including the wiring in a Meccano, skeleton-like structure,” the TfL manager said. “That allows Bombardier to test the systems and the software before trains have even been built.
“It also means that it’s a controlled environment. When you get changes coming through you can test them on train zero first before they go onto a real train. It’s used extensively in the aerospace industry and it’s a great innovation that I’ve not seen before on other rail projects like this.”
Crossrail is proof the rail system is not fragmented
It’s perhaps to be expected that a modern rail project should be delivered with modern technology. But as Sherrin explained, a modern attitude was also central to TfL’s success with the Elizabeth Line trains.
“The level of co-operation and collaboration with everyone on the project has been incredible,” he highlighted. “It’s been a success so far because of the way Bombardier, MTR, Network Rail and TfL have all worked together in a very co-operative way.”
The TfL project manager concluded that, on one level, the project had been a success due to the level of testing Bombardier had done. But ultimately, it was what Sherrin described as “the culture of co-operation and working together as a team” that was vital to a successful programme of works.
“Often in this industry you read some of the articles written by commentators and it makes it seem that we have a fragmented rail system,” he said. “But this project stands out as a real example of people working together.”
If there’s a lesson to be learnt from the delivery of the Elizabeth Line, it’s not simply that good rolling stock needs to be modern and well designed. Instead, it’s that teamwork between staff in every part of the system is essential, and that perfecting minor details (dodgy windscreen wipers and all) is crucial to a smooth series of works.
For more information
W: www.crossrail.co.uk
© Alvey & Towers